Injection molding is one of the most productive techniques for shaping materials. Until recently, injection molding was restricted to thermoplastic polymers (polymers that melt on heating). However, metals have property advantages over polymers. They are stronger, stiffer, are electrically and thermally conductive, can be magnetic, and are more wear and heat resistant. The concept of metal injection molding (MIM) combines metal powders and a thermoplastic binder to allow shaping of complex objects in the high-productivity manufacturing setting associated with injection molding. After shaping, the metal powders are sintered to densities close to those listed in handbooks; that is, they have very few pores. Accordingly, the process delivers materials with metallic properties in an efficient manner.
Metal injection molding, and the related process of ceramic injection molding, is a derivative of powder metallurgy. Metal powders can be shaped in a semi fluid state (powders that are poured into containers take on the shape of the container), but after heating to high temperatures the particles bond into a strong, coherent mass. In ceramics this is analogous to the manufacture of clay pottery, where shaping occurs with a water-clay system at the potter’s wheel, but after kiln firing, the structure is strong and rigid.
Metal injection molding is a process in which metal in a powdered form is combined with a polymer binder to produce a homogeneous mixture known as feedstock. The feedstock is processed in a manner similar to plastic injection molding, except that parts are designed slightly larger to account for shrinkage during the final sintering step. The molded part is called the “green” part.
Once molded, three methods are available to remove the binder from the green parts: solvent, thermal, and catalytic debinding. Differences in these methods affect the outcome of the product. The debinding phase can be the most time-consuming aspect of the process. After debinding, parts (known as “brown” parts) are sintered — a process in which the components are exposed to heat over an extended period.
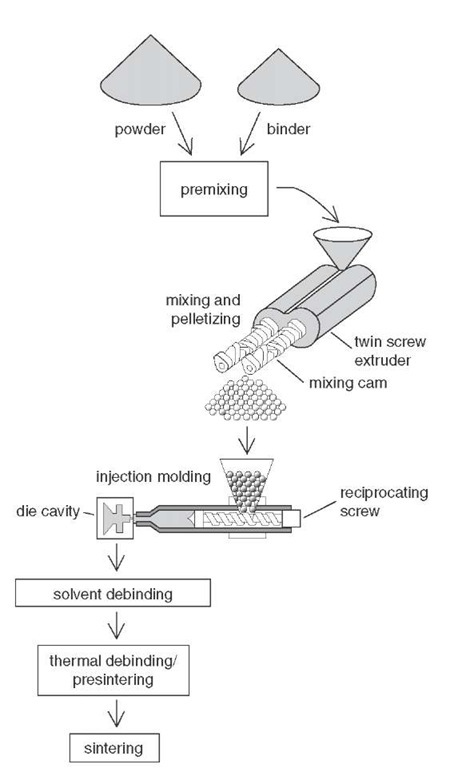
Applications
Metal injection molding is applied in the production of high-performance components that have complex shapes. The most successful applications involve components that have complex shapes and also must be inexpensive to produce while providing high relative performance. Generally, metal injection molding can be used for all shapes that can be formed by plastic injection molding, especially for very small complex geometries.
Many applications have been developed for metal injection molding. They include components for use in diverse fields ranging from surgical tools to microelectronic packaging. Recently, automotive components such as sensor parts in the air-bag actuator mechanism have moved into production. The technology has been extended to utilize a wide range of materials, including steels, stainless steels, nickel, copper, cobalt alloys, tungsten alloys, niobium alloys, nickel-base superalloys, and intermetallics. Additionally, most ceramics can be processed in the same manner; these include silica, alumina, zirconia, silicon nitride, silicon carbide, aluminum nitride, cemented carbides, and various electronic ceramics.
Although metal injection molding is generally viable for all shapes that can be formed by plastic injection molding, it is not cost competitive for relatively simple or asymmetric geometries. Large components require larger molding and sintering devices that are more difficult to control. Accordingly, metal injection molding is largely applied to smaller shapes with masses below 100 g.
As the engineering community better appreciates its favorable attributes, metal injection molding applications will grow. Although the current industry is relatively small, the anticipated growth is impressive. One area of keen interest is in the processing of titanium alloys for biomedical applications. Another is in the co-molding of different materials, that is, forming part of a component from one material and then another portion from a second material. This option has merit for forming corrosion barriers, wear surfaces, and electrical interconnections in ceramics. Other major growth areas include high-performance magnets, technical ceramics, materials associated with heat dissipation in electronic circuits, hard materials, ultrahigh-strength metals, and biocompatible materials.